MVP Launches Fast Flow LRTM Process to Speed Closed Mold Part Production
Knoxville, Tenn., August 17, 2020 – Magnum Venus Products (MVP), a global manufacturer of fluid movement and production solutions for industrial applications, is launching a new process for closed molding to increase part production by decreasing injection times. The new technique, aptly named Fast Flow LRTM, is a blend of MVP’s Flex Molding Process and Light Resin Transfer Molding (LRTM) and utilizes collapsible resin channels for a faster resin flow.
The process was brought about by the need to meet faster cure times for large parts using high viscosity resins such as fire retardant materials. Further trials and testing are currently underway with a large automotive manufacturer.
When using a traditional LRTM mold, the resin flow speed is dependent on the distance between the resin channel and center of the part during injection. Utilizing the same silicone collapsible resin channels developed for the Flex Molding Process, MVP’s Fast Flow LRTM technique uses a unique channel arrangement allowing channels to be installed closer together to decrease the resin flow distance and speed up injection times. This process is capable of injecting a fifty square-foot part in under four minutes using only one injection port, while also delivering a good back side surface aspect equivalent to traditional LRTM. By injecting the resin from the center to the border, the part demolds with a finished look and no visible resin channels, wasted materials or excess resin.
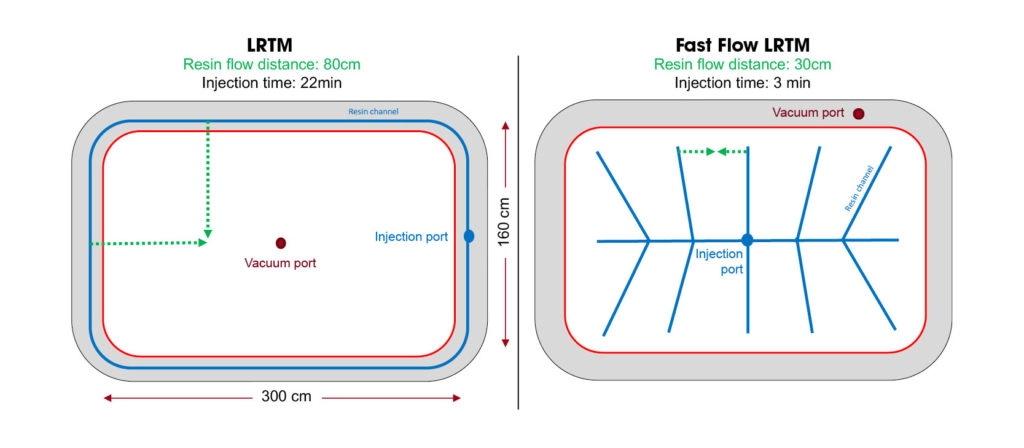
In the Fast Flow LRTM process, the female mold is constructed like an LRTM mold, but there are some key differences in the counter mold construction. It’s built with a silicone skin including a collapsible resin channel, then reinforced with composites. For this step of the process, MVP has developed a unique solution for bonding composites to silicone. The rigid counter mold provides a good quality back side surface, while the silicone membrane shows the reinforcement of the produced part.
MVP has been a long-standing leader in closed mold technology for decades with the developments of key techniques and accessories to complement its advanced injection equipment. The MVP technical support specialists travel the globe to offer comprehensive trainings and educational opportunities for manufacturers to learn more about closed molding procedures and techniques.
To learn more about Fast Flow LRTM, email info@mvpind.com.
About MVP
Magnum Venus Products (MVP) is a global manufacturer of fluid movement and production solutions for industrial applications in composites and adhesives markets. MVP collaborates with its customers to offer tailored production solutions to meter, mix, dispense, and apply materials. For over 80 years, MVP has been a leading equipment provider for the marine, infrastructure, pool and bath, oil & gas, transportation, aerospace, and wind industries. Learn more at mvpind.com.