The Lion’s Den
Protocol Conversion Gives Factories An Edge To Stay Ahead
Business leaders understand that the thoughtful integration of technology is key to acquiring and maintaining a competitive advantage. Only by staying ahead of the technology curve can a company stay in business. Accomplishing this in the Digital Era means leveraging automation solutions that decrease costs, enhance efficiencies, and maximize productivity. Manufacturers that wish to remain competitive must adopt digitization and automation across their operations, or risk being outperformed by rivals who invest in the technology.
A 2017 PriceWaterhouseCoopers survey of industrial companies titled Digital Factories 2020: Shaping the Future of Manufacturing found that 6% of polled companies had already fully digitized their factories, 85% responded that they use digitization widely, and 41% are using some standalone digital solution at their facility. Utilizing innovative technologies is a must for industrial organizations, but integrating these solutions can represent a significant capital investment. Even more challenging is the brisk evolution of technology which threatens to render solutions (equipment, operations, systems, etc.) outdated after they’re implemented, limiting ROI. How does a company enhance operations and keep pace with accelerating technological change in a way that is cost-effective? The solution: protocol conversion.
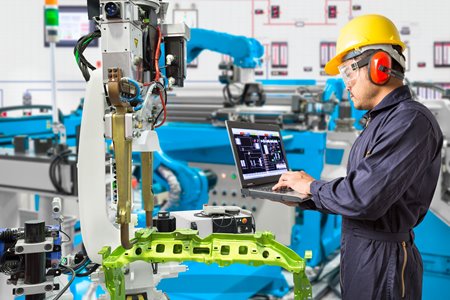
Protocol conversion involves connecting existing assets so that they communicate with one another, allowing a company to get the most out of their legacy equipment. While older machines may not have been designed for interoperability, protocol conversion can unite the assets and upgrade both their controls and motion to improve their manufacturing and management capabilities. Protocol conversion enables industrial machines to aggregate data in order to drive optimization. The data that is compiled can be monitored and analyzed to generate actionable insights, predict maintenance interventions, and minimize equipment downtime. By connecting legacy equipment for interoperability and utilizing Industrial Internet of Things-enabled technologies to upgrade or retrofit factory devices, companies can avoid having to rip and replace assets, promoting a fast ROI.
With over forty years of experience, Red Lion Controls is a global leader in communication, monitoring and control for industrial automation and networking. We provide proven resources for optimizing existing factory infrastructure through automation and M2M technology. Our solutions for protocol conversion can improve industrial operations using a balanced and flexible approach that is cost-effective. We facilitate a seamless transition from a traditional factory to an advanced network infrastructure, all with minimal downtime. Visit us here to learn more about our industrial automation products that can help your organization stay competitive.
Visit us at www.redlion.net to learn more
Read more at redlion.net