What are the Advantages of a Case Erector with Robotic Arm Movement?
The robotic arm has a long history in manufacturing. Now it has made its way into secondary packaging lines. When you look at the robotic arm on even a simple machine like a case erector, it has the power to inspire. Both in its resemblance to human form and futuristic nature, it promises to combine the best of human and machine movement.
A robotic arm functions and operates much like the arm of a human, with joints that can move in different directions. As the robotic arm picks and places, maneuvers and builds, it offers something that most other machines cannot: Simplicity. Instead of inventing a new machine process, the robotic arm is a replication of an already perfected all-purpose tool. Of course, robotic arms have been around since the 1960s, starting in automobile manufacturing.
But today, because of advanced developments, it’s now feasible and cost effective to deploy them in smaller applications, including secondary packaging. INSITE Packaging uses robotic arm movement to make end-of-line packaging more hands off and efficient, but it’s also something of a disruptor in the manufacturing space, says Todd Davis, manager of INSITE Packaging.
But when it comes to making capital investments, it always boils down to ROI, and it’s no different when you’re talking about a case erector with a robotic arm operation. Here are some questions one might ask:
- What advantages are there to a robotic arm movement in a case erector?
- Will you need a robotics specialist on staff to configure the case erector?
Robotic machinery is gaining ground in food manufacturing
First, here’s a quick look at the trends. Robotic automation is gaining traction quickly, even more quickly than anticipated.
Back in 2014, PMMI’s Trends and Advances in Food Packaging and Processing report forecasted that 82% of manufacturing plants in the U.S. would be using robotics. In 2019, it reached 90% and in the coming five years, a manufacturing floor with at least some robotics will be almost universal.
As this Packaging World article indicates, the higher output driven by COVID-19 at food companies is feeding a demand for robot automation, from producing to packaging all the way down to end-of-line secondary packaging. The reason: Increased concern for employee safety coupled with the overall growth in the food industry.
Advantages that robotic arms offer in case erector applications
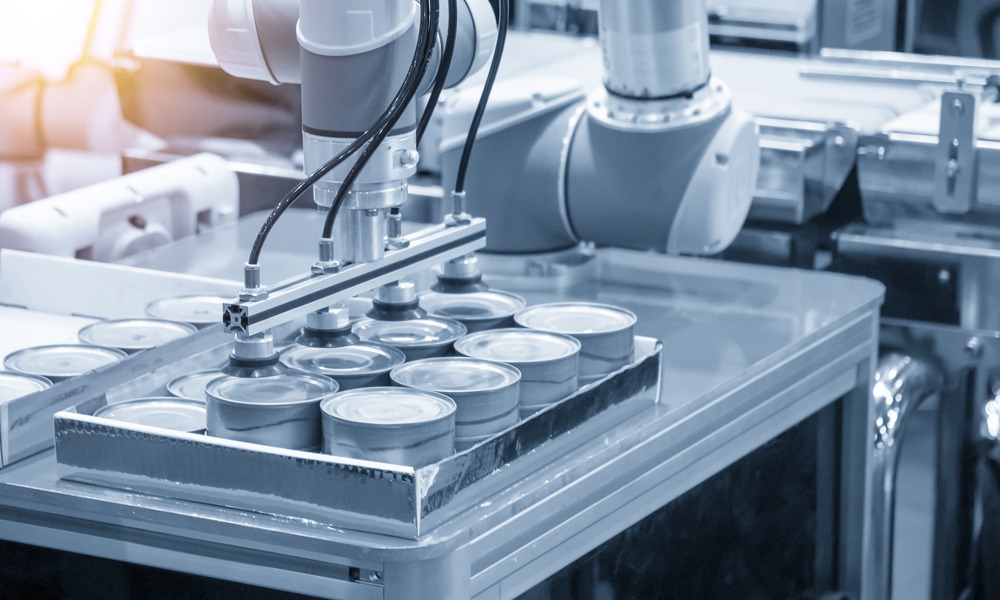
Accommodating increased SKUs
In today’s market, that’s more critical than ever, as 67% of food manufacturers report a marked increase in SKUs, according to the 2019 Trends and Advances in Food Packaging and Processing. It goes on to detail the top challenges that accompany meeting production demands.
- Increasing yields with existing equipment
- Finding greater efficiencies in production processes
- Integrating automation
- Keeping up with changing market and retail demands
- Maximizing uptime with reliable machinery
“This comes up frequently with our customers,” Davis says. “Marketing teams invest a lot into the product, finding the perfect shape and graphics for the packaging to give it differentiation. But what’s troublesome is the life cycle of products is getting shorter, and that might make some equipment obsolete. That’s why we deploy robots.”
[Check out Hip to be square: The benefits of active case squaring]
Meeting retailer requirements
When we’re talking about case sizes, there’s no such thing as one size fits all, not when case counts and product sizes wildly vary, depending on the requirements and product needs of the retailer. That points to the struggle with increasing yields with existing equipment, especially if its design isn’t conducive to repeatability and fast changeovers. More than ever, food manufacturers need flexibility from their end-of-line equipment.
Meeting labor needs
When humans are assembling boxes, it’s brain-numbing work. It’s repetitive, it can lead to repetitive strain injuries, and arguably offers little in the way of job satisfaction. Robotic automation offers that same flexible ability to set up cases of any size, so employees can work more productive and rewarding jobs.
Higher repeatability and less maintenance
“If you have a recipe to run different case sizes, once you select that recipe, the servo motor knows exactly what to do and repeats that over and over, with a high degree of accuracy,”
When it’s time to change case sizes multiple times during a shift, one ongoing issue is achieving a high rate of repeatability — one of the challenges that presents itself as production schedules adjust to accommodate additional SKUs to meet market and retailer requirements. That’s where a traditional case erector can interfere with uptime and overall efficiency. Case erectors are driven by air cylinder operability. These are inexpensive, but the air cylinders are in need of frequent replacement and maintenance, making it more difficult to achieve consistent repeatability.
In addition to the need for frequent replacement, “The air cylinder is not a high degree of accuracy type of device,” Davis says.
INSITE’s case erector replaces these mechanical movements with a SCARA robot, drastically reducing the number of air cylinders and as well as the components, by 50%. Fewer parts means less focus on maintenance, and the SCARA robot comes best-in-class repeatability.
“If you have a recipe to run different case sizes, once you select that recipe, the servo motor knows exactly what to do and repeats that over and over, with a high degree of accuracy,” Davis says.
[Check out Get to know your case erector and sealer: Top features of INSITE Packaging robotic design]
Ease of operation
One hurdle to adopting robotic automation is the lack of expertise about programming, Davis says, which can make some manufacturers hesitant to adopt this technology.
An old-school guy might look at the robotic arm, and be a little concerned: “I’m used to the older machines and all their parts, with them I know what’s going on. This machine, that’s a new learning curve. I’m sure it means I might need to know programming.”
“That’s where the software tools are there to fill that gap and allow you to essentially control the robot,” Davis says. “There’s no need to worry about programming the robot. Our servo-driven robotic arm is controlled through our HMI (human machine interface).
“When we change the case size through the HMI, the software tells the robot what new path to follow,” Davis continues. “So the end user doesn’t have to figure out the complicated aspect of creating a robotic path to follow. It’s all software driven. People don’t have to go through the basic setup. The software takes care of it.”
A case erector with a robotic arm operability can raise repeatability and lower your overall maintenance needs and expenses, giving your machinists more bandwidth to focus on more critical areas on the production floor.
Contact INSITE Packaging today and start seeing the benefits on your line.
Follow us on social media for the latest updates in B2B!
Twitter – @MarketScale
Facebook – facebook.com/marketscale
LinkedIn – linkedin.com/company/marketscale