Honeywell Has a New Urban Air Mobility Lab. Why Does Its Avionics Research Matter for UAM?
Summary: Honeywell unveiled its cutting-edge urban air mobility research facility for a closed media tour. MarketScale had the pleasure of exploring the company’s new technologies to better understand how they’re setting a standard for UAM’s avionics needs. The main solutions on display and detailed in this report include its Simplified Vehicle Operations controls interface, its Detect and Avoid Radar solution, and its small form-factor fly-by-wire digital computer.
Table of Contents
- A Brief Honeywell Avionics History Lesson
- Simplified Vehicle Operations
- Detect and Avoid Radar
- Compact Fly-By-Wire System
- How Will Honeywell Stand Out in a Crowded Field?
- How Can Honeywell Strategically Bring These Technologies to Market?
Nestled into arid Phoenix, Arizona, deep in the stretches of its business parks, sits Honeywell Aersospace, the aircraft engines and avionics division of Honeywell International and just one of the many arms of the multinational manufacturing and business solutions conglomerate. The company at-large has a global footprint that touches a number of critical industries; from building management, to last mile software delivery solutions, to inorganic chemical compounds. Though, under its Phoenix roof is maybe the company’s most exciting, cutting-edge and future-focused research: developing new avionics solutions in urban air mobility.
MarketScale was invited to visit Honeywell’s new UAM lab for an exclusive media and analyst tour, one of the few times third-parties have laid eyes on Honeywell’s UAM work and the facilities enabling it. Both a showroom and an active research center, the UAM lab’s most current form was developed less than a year ago with the express purpose of assessing the most pressing trends and technologies shaping the future of air mobility.
“Even the whole lab here is meant not just for show and tell, but this is actually going to be a development where our lab engineers are going to be coming and actually working on the product,” said Sapan Shah, product lead for the UAS/UAM division at Honeywell Aerospace.
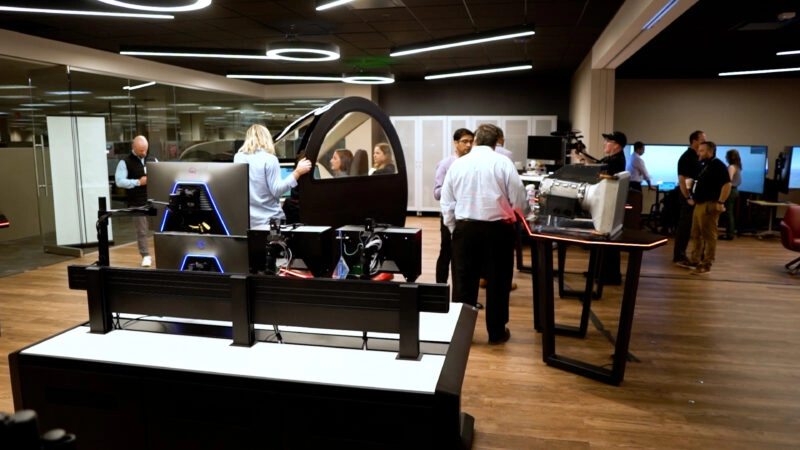
Why invest so heavily, with both solutions and an entire research wing, in this specific side of the aerospace industry? And why now? A vision for ‘flying cars’ has been an American staple as early as when traditional automobiles were still gaining mass acceptance. As air travel became a popular part of everyday society in the mid-20th century, and as 1960s-styled science fiction visualized a futuristic urban air network for consumers, the idea of realizing short-distance urban air travel suddenly felt less like a pipe dream for OEMs and private services. The back half of the 20th century saw several attempts at realizing this vision with helicopter air taxis, but everything from price barriers to fatal accidents tempered the energy behind UAM.
The hunger for UAM has been there, but the technology and policy ecosystem just hasn’t been able to support the industry. Today, the desire for UAM is increasingly defined by urban realities: a COVID-accelerated suburban sprawl coupled with a mass return to the office, more visible climate change in major metropolitan hubs, and the growing production of electric vehicles reigniting the imagination for cleaner and elevated transportation…pun intended. And finally, the technology needed to make UAM a reality is closer than ever to our collective imaginations.
“I think urban air mobility, the story is really a technology story, but it’s also a story about society and society at large,” said Daniel Newman, principal analyst and founding partner at Futurum Research and one of the guests at Honeywell’s UAM lab unveiling.
“And so the idea of being able to move people more efficiently is a story that probably isn’t being talked about enough because we tend to like to focus on the tech, and as a tech analyst, I love to focus on the tech. But I think in the end, it’s going to be about how do we really improve people’s lives? How do we improve society, drive more productivity and of course create a stronger economy?”
This societal craving for bringing the world into ‘the future,’ as well as the potential for reaping massive profits in an untapped market, has finally culminated in the urban air mobility research we see today. Led by commercial drone usage and the development of vertical takeoff and lift aircrafts, UAM as a formal industry is now categorized by the FAA as a “safe and efficient aviation transportation system that will use highly automated aircraft that will operate and transport passengers or cargo at lower altitudes within urban and suburban areas.”
Bringing this aerospace sub-industry from concept to reality takes not just new vehicles and new regulations, but an entire ecosystem of technologies that will manage autonomous flight, collision detection, and vehicle operations. A full suite of avionics for an emerging industry is Honeywell’s bread and butter and it’s where Honeywell is most needed in supporting UAM growth.
From the First Autopilot to Supporting Autonomous UAS
As Newman sees it, bringing in media for a lab tour was as much a marketing endeavor for Honeywell’s new research as it was a desire to recontextualize Honeywell’s experience in avionics. Though it’s a point of pride for the international conglomerate, its avionics don’t always get the B2B pat-on-the-back they deserve, let alone the consumer recognition.
“A company like Honeywell that often is in the background, they are making a ton of meaningful contributions to the aerospace industry, one of the leaders in the space, but not always recognized. We recognize the carriers, we recognize the jet makers,” he said.
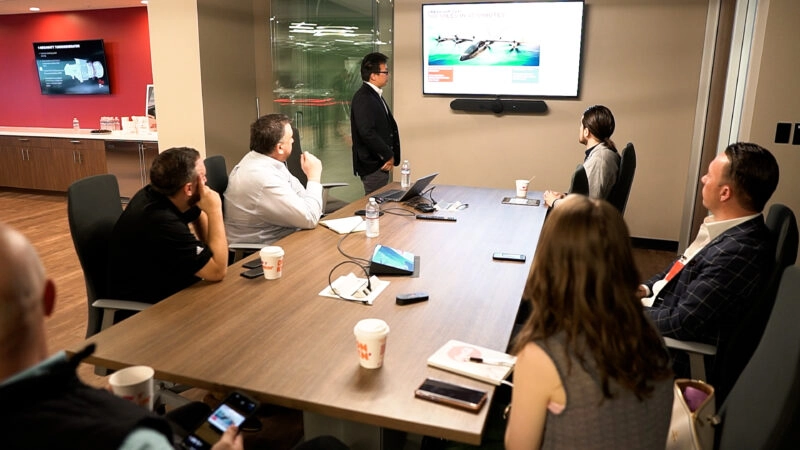
Honeywell’s history in avionics is robust; the company first entered the commercial space in the mid-1950s, and was developing avionics for military aircrafts as early as World War II. Its milestone achievements include inventing cabin pressurization, the autopilot control system, ground proximity sensors, and featuring their display and engine controls on the Apollo 11 rocket. It’s that history of avionics innovation, success and imagination that gives Honeywell the pedigree to tackle UAM solutions.
“When we talk to customers, we’re not only saying, yes, we can solve that particular problem, but we’re not just going to give you something and you’ve got to figure out how to integrate this in your system. Because Honeywell has such a long legacy of developing all these products, both mechanical, electrical, propulsion, we have the ability to not just say, here’s a piece, but here’s the whole puzzle that piece goes into,” said Monta Fowlkes, senior business director for UAM/UAS at Honeywell Aerospace.
Honeywell launched its UAM division during peak COVID-19 in June of 2020, and from the start, identified its role as leveraging the “power of our engineering resources and know-how to transform urban air taxis, drone delivery of parcels and all forms of autonomous flight.”
The high-level challenges still in front of fully-realized UAM deployment are numerous, but Honeywell’s focus in launching its UAM division and lab lands on three main factors: creating technology that removes risk, creating smaller avionics solutions, and collaborating on needed policy.
“As much as we want to make sure we continue to up-skill the human workforce, keep people involved, pilots take on a lot of risk and flying has become more and more autonomous. But in in the most dangerous situations, policy is going to really matter because you can train in a simulator your entire life as a pilot, but that first time you lose an engine or that first time that a bird flies in and it causes a major disruption, how ready are you really for these situations,” Newman said.
“You want to be able to take what you have in a much larger aircraft and be able to put it in something that’s more of a personal size, but also have it in a way that it’s affordable,” Fowlkes said.
Though UAM is its own sub-industry of the larger aerospace industry, it itself has specific core segments that are shaping use case and technology research: urban air taxis, middle-mile cargo, and last-mile delivery. At Honeywell, the aim is to meet the needs of every segment with one focused research and development campaign.
“We’re able to address several different markets and a lot of cases with the same types of solutions,” Fowlkes said.
The drone space is Honeywell’s first priority, considering the complexity of the systems needed to maneuver drones is much simpler, lowering the barrier to entry for both tech-validating use cases and new regulation to manage a growing network.
The vehicle size required for middle-mile cargo is a good transition point for Honeywell’s research to go from the smallest of form factors to some of the largest in UAM. Not for nothing, the public perception around larger vehicles flying over crowded urban environments is mixed. Surveys show that while consumer support for UAM is strong, even stronger is their concern for the safety of civilians on the ground. Again, this makes drones and middle-mile cargo a more attractive first endeavor.
“From a safety perspective…people would be much more comfortable with autonomous cargo vehicles flying around versus something with urban taxi that actually has people in it,” Fowlkes said.
In the air taxi space, Honeywell boasts important partnerships with the OEMs developing popular VTOL prototypes, like Pipistrel, Lilium, and Textron. Though middle- and last-mile research is more immediately applicable, Honeywell’s product development is all leading towards enabling the ‘flying car’ future we’ve imagined for decades.
While touring the lab, MarketScale had a chance to sit down with various team leads to dig deeper on the specific technologies Honeywell is bringing to market. As we’ll explore below, each solution is solving its own challenge in UAM while also integrating with a larger ecosystem of avionics. It’s Honeywell’s speciality, and the results of its research are already exciting.
“We see ourselves as enablers,” Fowlkes said.
Simplified Vehicle Operations
What Is It?
When you first enter Honeywell’s UAM lab, it’s hard to miss the massive space shuttle-looking cockpit in the middle of the facility. Thinking it’s the main attraction, you might take a seat and admire the reflective surfaces and the modern form factor. Honeywell’s new technology of note, though, isn’t the sleek cockpit itself but the bells and whistles on board, the avionics powering an upgraded and simplified dashboard experience.
Known as Simplified Vehicle Operations, or SVO for short, this Honeywell solution is working to drastically simplify and improve the entire array of flight controls and instrument panels, from screens and meters to gauges and lights, that make up today’s modern cockpit. Airspeed, heading, vertical speed indicators, turn coordinators, attitude and altitude meters, and the yoke make up just a few of the basic instruments that define aircraft piloting; Honeywell believes all these controls, and the dynamics between them, are up for innovation and improvement.
“Essentially what we do is we take the pilot and deconstruct the pilot into a lot of different functionalities,” Shah said.
Even as the digital transformation of the cockpit has already simplified and replaced a lot of the old physical gauges with digital meters and systems, the intricate relationships between each indicator can take hundreds if not thousands of hours to fully grasp.
“One of the examples people like to use a lot is the idea between an automatic transmission and a manual transmission…. You get behind an automatic, now I can drink my soda while I’m driving,” said Fowlkes. “So it doesn’t take very long before you say, ‘I see the advantage to this.’ Anytime you’re reducing complexity and making it more intuitive, I think it’s natural for people to say yes.'”
As an alternative to the traditional suite of avionics, Honeywell’s SVO condenses cockpit controls down to a set of touchscreens and an inceptor. Leveraging a full suite of solutions from Honeywell’s detect and avoid radar to its fly-by-wire computing system (both of which we’ll explore in depth below), the new dashboard aims to introduce a higher level of autonomy, ease of use, and visual intuitiveness to piloting.
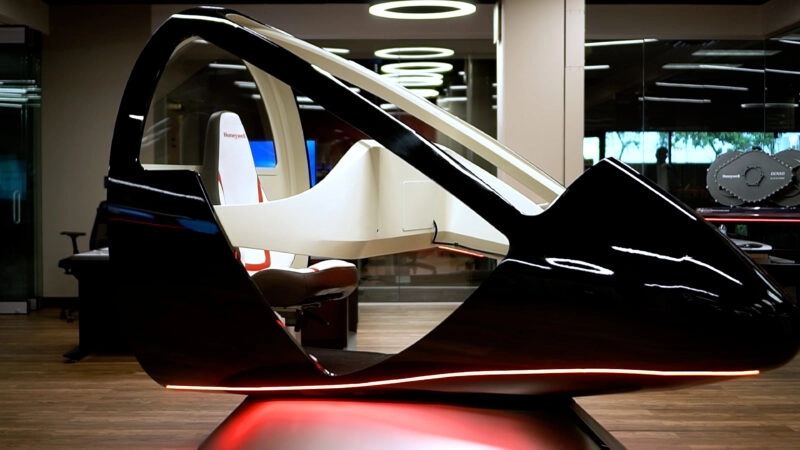
Whereas before, a pilot might use a rather cluttered and convoluted waypoint navigator to guide their minute-to-minute decisions and stay on course, with SVO the pilot would reference a 3D-rendered environment of their flight path, reflecting geographic terrain, landmarks and even roadways. Honeywell’s vision was to look to consumer electronics for visual inspiration, which have been perfecting simple navigation interfaces for years now. In bringing that ease of use to the cockpit, it would ideally remove confusion and minimize human error while in the air. The entire experience was reminiscent of plugging in an address over CarPlay, with a touchscreen, sleek GUI and all.
“You no longer have cryptic waypoints; you have road names. So if you are an operator flying in Phoenix every day, you look at this and you know exactly what these are, and you look down and you know where you are. So you’ve got that situational awareness,” Shah said.
Like playing a Quidditch mission in a Harry Potter video game, or following your route on Google Maps, pilots would have an almost gamified guide highlighting their path from point A to point B. Add on top of that a layer of automation that keeps the vehicle to a strict altitude and heading, piloting an SVO-powered plane would make it much easier to keep to a pre-determined flight plan.
“The other innovative thing that we’re addressing is essentially to have the skylane or highlane…just like when you’re on the road and you have the white and yellow lines, I think that just provides a lot of situational awareness of where you are, how fast you’re moving, where the other vehicles are,” Shah said.
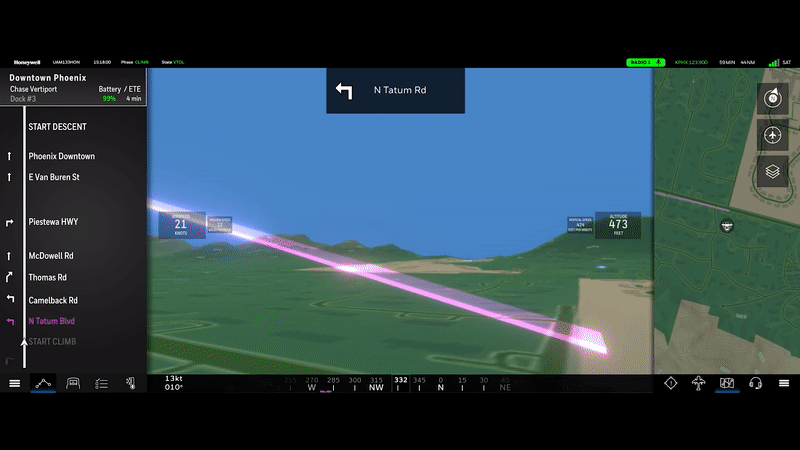
Most, if not all, commercial airliners today have robust and capable autopilot functionality that can balance the relationships between each flight control. It manages cockpit workload and usually performs tasks more quickly and efficiently than the average pilot. However, two areas are still prime for autopilot improvement:
- Smaller aircrafts, from private single-seat aircrafts to 20-seat jets, still don’t have a standard autopilot solution.
- Existing autopilot functionality still requires constant monitoring and cross-checking from pilots.
The vision for Honeywell’s SVO is to solve both of those challenges, making autonomous functionality simpler, more responsive and less manned. Honeywell still has a lot of work to do before said autopilot technology can can claim to be “fully autonomous” and the FAA will likely still require pilot redundancy for vehicles carrying passengers. Autopilot, for the foreseeable future, will need the watchful eye of a pilot. However, getting its functionality to a point where it’s confidently a more present part of minute-to-minute UAM piloting will naturally bring down possibilities for human error, and if Honeywell sticks to its standards, it would be a major upgrade to the capabilities of traditional autopilot systems.
“The autopilot is always on. You never turn off the autopilot…which is very different from today’s vehicle, where there’s a lot of mode confusion, and that causes accident. Is the autopilot on or not? Do you know what is on and not on?…. If you look at the accident reasons, those are some of the reasons for that. And what we have created here is that you can fly a vehicle coupled to a flight plan,” Shah said.
Clear yet simplified indicators and a road-based GPS navigation system would make for a familiar experience behind the yoke. Though this is being developed for less-intensive piloting operations like air taxi-style vehicles, the idea is still to scale the solution for commercial flights. To prepare for that long-term adoption, Honeywell is building flexibility into the pilot-automation balance. Essentially, pilots can choose which features to couple with the pre-determined flight plan and which to manually control. There are some guaranteed limitations, though; for VTOLs at least, the automation features would include safety boundaries. For example, pilots won’t be able to do a barrel roll and flip the vehicle upside down, no matter how hard they crank the inceptor.
Pilots will still want manual functionality, though. What if there’s an unprecedented obstacle suddenly in the way of your aircraft, right along the pre-determined flight path? Shah and his team are working to solve this with SVO, too. Whether it’s a manual override from the pilot, a new flight path from an independent operations control center or a more formalized ATC-style network of oversight, SVO would allow for in-flight redirection without losing automated functionality.
“Let’s say President Biden is in the area unannounced, and now there’s airspace restriction…or there’s a law enforcement helicopter, and you can’t go there. There will be a lot of reasons where there is an airspace restriction suddenly. So yes, you will get an uploaded flight plan and new flight plan where you say, ‘you have received a new flight plan, activate.’ All you have to do is press activate and you don’t need to fly around it…that new flight plan becomes your primary flight plan,” Shah said.
Why Research It?
Honeywell chose the goal of innovating critical aircraft controls as a key research focus due to an intersection of important trends shaping the growing UAM market:
- a pressing pilot shortage, exacerbated by the pandemic and the macroeconomic environment
- a growing interest across the world to develop a network of VTOL aircrafts, and the corresponding infrastructure, for urban air travel
- a desire to capture VTOL market share pushing aircraft manufacturers to more heavily invest in research and development of UAM solutions
“If you look at all the OEMs that are talking about the operations of the next five years, they’re all looking at ramping up to thousands of vehicles very quickly…because there’s definitely demand out there. And in general, for every aircraft, you need about three to five pilots. So if you’re looking at 5,000 vehicles, that’s about 15,000 to 25,000 pilots. And we already had a pilot shortage pre-COVID,” Shah said.
Training pilots is already a massive undertaking. The FAA currently requires a varying minimum of training hours depending on what kind of piloting you’re preparing for. A recreational pilot only needs 30 hours to get certified. A commercial pilot needs closer to 250 hours or so. Airline pilots need as much as 1,500 hours of training before they can get in the cockpit. The current pilot shortage is already putting pressure on these requirements, and they’re likely to face further critique as the UAM market begins to take off.
It’s still not decided which pilot license would cover a standardized set of vehicles like air taxis, but regardless, the possible scope of training investment to launch a nationwide VTOL network is seen as too inhibitive by industry players, from airlines to Honeywell.
“How do you get somebody 1,200 hours, because that’s what’s required by FAA in order for you to actually fly? Now you need 20,000 pilots with 1,200 hours. And it takes two to three years for somebody to get there. That’s a tremendous amount of training, cost, work associated to make the ecosystem work,” Shah said.
By introducing robust automation, Shah imagines a world where operational energy, and therefore training, is cut down considerably for pilots. If pilots are now focusing their training on situational awareness, contingency management and strategic critical thinking, rather than the nuances of complicated control relationships or the manual operations that come with those nuances, would a pilot still need that level of training? Shah says no, detailing a future where pilot training can be cut down by as much as 80%.
“By providing technology and automation, now you’re changing a two-year cycle into a six-month cycle,” he said.
To both travelers and pilots, it might seem strange to want to simplify aircraft operations down to a gamified, consumer electronics-reminiscent state, even with a pilot shortage. Is tinkering with robust functionality, and a tried-and-true cockpit set-up, not too much of a disruption for the air travel industry? Apparently not. It turns out that even OEMs and pilots are pushing for this sort of cockpit upgrade.
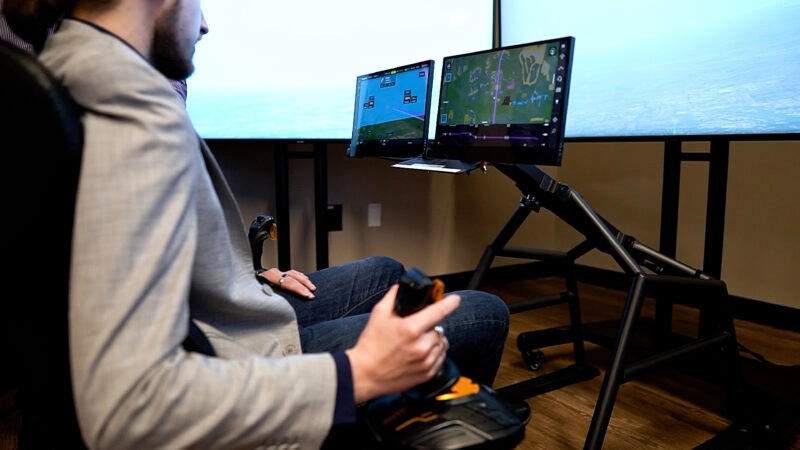
“I was talking with the chief test pilot with one of our customers and he said, this was within the first 40 minutes of all the meeting, he’s like, ‘I love it when we just agree with everything.’ Because he sees that vision, he sees the vision of simplified vehicle operation. He sees the vision of unified flight controls…whether you’re going in a vertical flight or a forward flight, your controls are mapped in such a way that it’s intuitive for you,” Shah said.
“We’ve gotten pretty good response from that, even today we’ve shown this to a couple of pilots, and they’ve said, ‘Hey, I want this, this is great,'” Fowlkes said.
Scaling VTOL operations with the current avionics standards will be an operational burden for new pilots, and the larger air travel and UAM industries recognize this coming challenge. Honeywell has been one step ahead of bridging that coming market with an improved cockpit experience; Fowlkes says the company has been the one to lead the charge among pilots and OEMs to reimagine the cockpit inside and out, anticipating massive UAM market growth over the next decade.
“The setup that you’ve seen today is almost entirely Honeywell driven, based off of early feedback we’ve seen…. So, we’re actually going to a lot of the actual aircraft manufacturers and saying, ‘we have a setup, we would like to propose it to you,'” Fowlkes said.
The core goal, even in reimagining the cockpit, is reimagining it in service of the pilots who’ll man the emerging VTOL service market. Creating a standard operating system that gets placed in just about every OEM’s cockpit is a lucrative and extremely profitable opportunity for Honeywell, but if it’s not a measurable improvement to the flight experience, it won’t meet the company’s stated goals and will likely fail to catch on.
“Our job is just to make sure that we match the interface that works for them. Are we putting things where they want? If they touch it this way, is that helpful? Is the response time in a way that works for them?” Fowlkes said.
How Will It Impact UAM?
To validate SVO technology and prepare it for mass market deployment, Honeywell is first designing it from the ground up for VTOL operations. While the long-run of SVO includes single pilot general aviation and commercial aviation, the still nascent VTOL market is the one most ripe with opportunity; an avionics solutions provider like Honeywell could set the controls standard for the entire future network of urban air mobility vehicles. All the company needs to do is get in with the OEMs, a task that shouldn’t prove too difficult for a highly-regarded avionics firm like Honeywell.
“All of the major players in the industry today are essentially building an air shuttle and air taxi,” Shah said.
The first use case for SVO is connecting different densely populated areas in major metroplexes; the lab’s SVO simulation was a familiar one for MarketScale, playing out a flight between the north Texas suburb of Plano and the DFW International Airport’s Hyatt Regency.
“The big use case here is going back and forth from a city center to a suburb, day-in and day-out. Essentially it’s an air taxi,” Shah said.
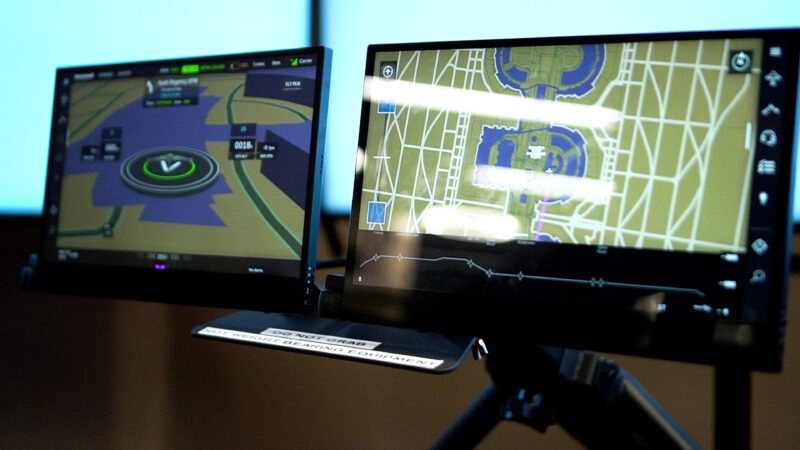
A key necessity for making SVO a reality is perfecting Honeywell’s detect and avoid (DAA) technology. Currently, DAA isn’t ready for SVO deployment; the radar tech, which we’ll break down next in this article, is being tested and designed for use in middle- and last-mile cargo solutions. That means at first, it’ll mostly be a situational awareness solution rather than a full automation solution. But getting DAA to be both an effective detection and avoidance solution will prepare it for SVO use, and when that happens, Honeywell believes the possibilities are endless for SVO validation.
“This is a proving ground for the entire aerospace. Once we have the solution certified and operational, there is no reason why a private pilot flying a Pilatus wouldn’t have this kind of technology,” Shah said.
Honeywell still sees several opportunities and challenges playing a role in determining the future of SVO deployments. Here are a few of the key areas, from policy concerns to technology visions, where Honeywell is focusing its attention for the future of its UAM avionics solutions:
- Vehicle-Agnostic Solutions: “Once you’re able to get more of a unified solution and one unified approach it couldn’t be too long before you learn to fly one aircraft and now suddenly, you’ve got the ability to fly a lot of different aircrafts, which isn’t that case today,” Fowlkes said.
- Proper Charging Infrastructure: “Most of these vehicles have a range of a hundred miles…. So I don’t see in the near term like a cross country thing because unlike Tesla, where you can just pull up and there are charging stations now everywhere, you might find a landing spot but there might not be infrastructure to charge the vehicle,” Shah said.
- Proper Flight Deconflicting Oversight: “Definitely in the beginning you would have a need to talk to the ATC, especially in the terminal area when you’re landing. But as the tempo increases, FAA has mentioned that ATC would not be able to handle the volume. And so, the requirement for talking with ATC should start going down significantly,” Shah said.
- Achieving DAA Certification: “In the beginning, we’re not going to have a certified solution that will allow the vehicle to automatically detect and then take over the flight to avoid it. So, we do have the technology, but it’s just going to go through the certification for a manned vehicle…. The radar can still be available. It will just detect the vehicle, but it will be your responsibility to then avoid it,” Shah said.
- Regulation: “Because the regulations are all built around existing Part 23 and Part 25 aircrafts…not all the products that we have may fit into that framework. And so, we need support from the OEMs…but also, the FAA, EASA, they’re going to help us navigate this,” Shah said.
- Working with Trade Organizations: “GAMA is organizing and hosting one of the industry groups for SVO…. Honeywell is taking a leading role in that. NASA is also an active participant in this,” Shah said.
RDR-84K Detect and Avoid Radar
What Is It?
As mentioned above, Simplified Vehicle Operation is as much a singular concept for a reimagined cockpit as it is an ecosystem of solutions supported by key interrelated technologies, all being researched and developed by Honeywell’s UAM team. One of the solutions that will be critical for fully-realized SVO, and more specifically its autonomous capabilities, is the RDR-84K system, a radar under strenuous testing at Honeywell’s lab. To the team, this solution is colloquially called the Detect and Avoid Radar.
“Radar has been deployed on plenty of drones, larger drones. This is the first time that a radar that we know of has been employed for an autonomous detect and avoid maneuver on its own at this small scale, these low altitudes and high speeds,” said Larry Surace, lead UAS & AAM systems architect for Honeywell Aerospace.
Situated in its own glass cubby in the UAM research facility, the DAA team’s workstation is littered with various drones, spare parts and flight-simulating computers; their research was some of the most active in the whole facility. Running all of its production in-house, from test-printing small parts to running flight tests, DAA puts a long history of Honeywell radar solutions to work by retooling algorithms, technology and expertise for a smaller form factor and more advanced use case, much like SVO.
“The pedigree of the technology goes all the way back to our air traffic control radars. We’ve learned algorithm development, radar development…that goes many decades back for Honeywell,” Surace said.
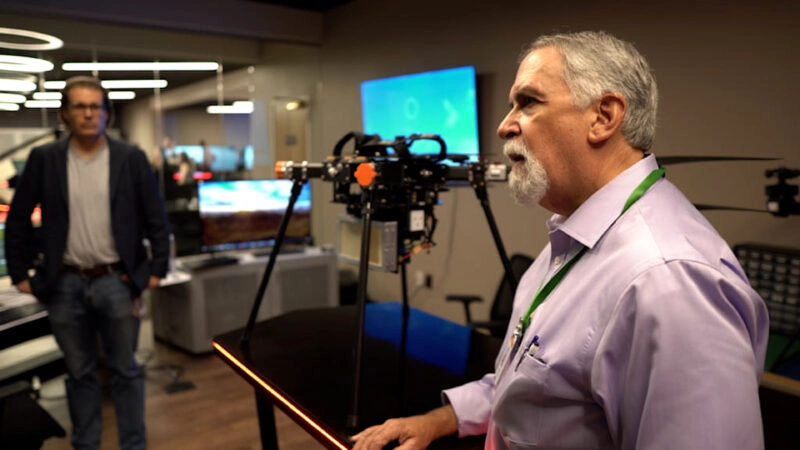
Also like SVO, DAA rocks an on-the-nose name that reflects its desired functionality: detecting and avoiding obstacles autonomously. By adapting a typical microwave-pulsing radar to also process object avoidance algorithms and act on them at quick speeds, the Honeywell UAM team is developing a radar that’s immediately applicable to all current and coming UAM vehicles, from air-taxis to last-mile delivery drones.
The solution is first being tested for drone applications, a more mature market with more immediate collision-avoidance needs. Like most solutions at the UAM lab, it’s still under development but has already logged several wins that are getting it closer to deployment.
Last year, Surace and senior advanced systems engineer Andrew Baker successfully performed an autonomous detect and avoid maneuver with a DAA-mounted BFD Systems drone. Flying against a non-cooperative intruder drone, the BFD drone was able to sense the incoming obstacle and move out of the way while at a low altitude and high speed. Though Baker was still behind the sticks as a supervisor, the DAA drone was consequentially able to steer around the intruder using only the data fed to the onboard flight control computer by the radar, all without Baker doing any intervention.
As Surace put it, that was a “real breakthrough” for the UAM team.
“That was a year-long effort that we went into, starting at the beginning of the year to do radar characterization integrated on a vehicle…and then characterize how well the radar actually performed in both cooperative, non-cooperative, open loop and closed loop,” Surace said.
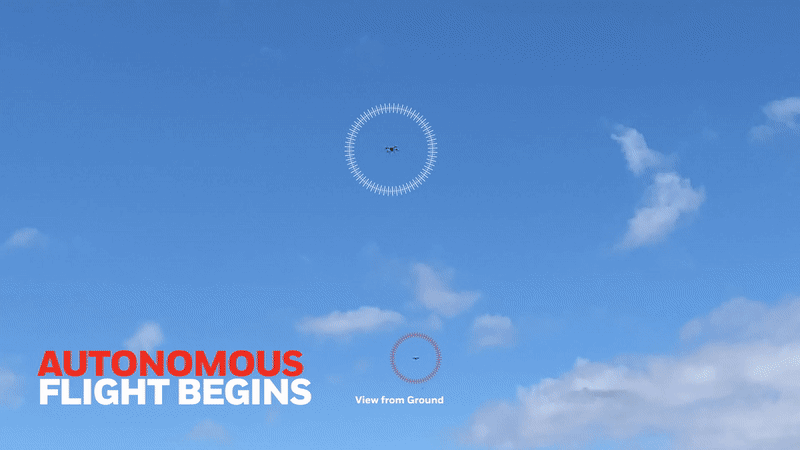
Getting the DAA solution to that point took more than one test and was filled with needed trial and error to refine the algorithms. Over the course of years, Surace and Baker pit the DAA drone against several vehicles (including an R44 helicopter) to make sure it could perform under different scenarios, like flying against a UAV at co-altitude, varying altitudes and speeds, and more.
As Surace and Baker refine the solution’s capabilities and performance, the same three metrics of success that defined their initial tests continue to guide their work.
“One was, how well does it work? Just get it working. How well does it work with the detect and avoid algorithm? And then how well does it work and steer the drone in the right direction,” Surace said.
Why Research It?
A Jetsons-style future that the casual public expects from UAM research and development is years away. Getting anywhere near a constant stream of airborne vehicles crisscrossing about densely populated global metroplexes is going to require efficacious autonomous capabilities. On-board AI will need trustworthy contingency management to support pilots and avoid collisions over urban areas; a whole community of professionals and citizens will depend on this AI even more, now that pressure is mounting to reduce the needed training for UAM vehicles and to make sure urban areas aren’t littered with falling UAV debris, respectively.
Before DAA can meet those needs though, it must perform for the already-growing fleet of drones entering the middle-mile cargo and last-mile delivery portions of the supply chain.
“Pipistrel being one of our biggest customers is going to be operating before the last mile becomes broadly adopted. Wing and others are operating in Dallas and Australia, so it’s happening…but in terms of a broad scale commercial use, we see that middle mile as well as last mile as a use case for this,” Shah said.
Partnerships between DroneUp and Walmart are bringing drone delivery to millions of US households, and across the seas, the EU is approving its first round of BVLOS drone operations for middle-mile cargo. For supply chain drones specifically, the need for detection and avoidance capabilities is pressing; since drones are finally being launched en masse for these use cases rather than in small regional pockets or small numbers, more obstacles in the sky means more dollars on the line and more safety concerns.
Honeywell’s goal is to define the hardware, which would then turn into a cooperative communication network for scaled drone deliveries. If the UAM team can anticipate the needs that come with scaling drone operations and create the trusted infrastructure for keeping operations safe, then it will give Honeywell a jumping-off point for bringing DAA to larger vehicles and larger stakes.
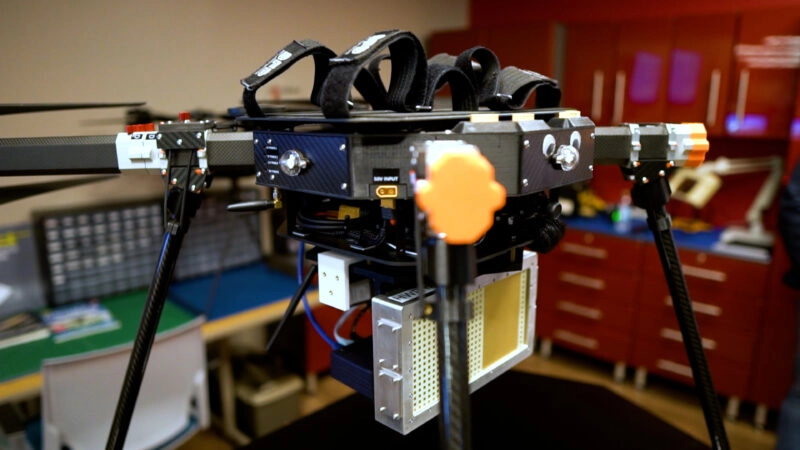
Today’s drone OEMs aren’t just concerned with guiding BVLOS regulation and securing important partnerships; they’re also in need of payload solutions that can actually weather the wear and tear of daily drone flights. Anything like an intelligent radar system will have to survive dynamic and unpredictable weather, debris, heat and the issues that come with operating on a lightweight and sensitive vehicle. Honeywell took on those challenges with its DAA work; since there was no blueprint, figuratively and literally, for mounting a small intelligent radar onto a drone, Surace and Baker had to do their own 3D printing of parts to test and refine the casing. The goal for the team was to introduce DAA to market with an already-existing mount, solving some of the basic customer needs and requirements for keeping critical payloads sturdy and safe.
“Putting [the radar] on a drone was not an easy environment. It was dusty, it was hot, it vibrated. Working and understanding how all those factors came together, working the body motion solutions, and then showing how it would detect the other target and get the detections to form tracks, building the timeline out. It was really test and trial, test and trial and working out the bugs,” Surace said.
How Will It Impact UAM?
For the foreseeable future, DAA will have its chief impact on middle- and last-mile UAM solutions, from small form factor drones to larger unmanned cargo vehicles. This isn’t just because of the timelier use case needs of a more mature market, but because the market is friendlier for testing and validating new UAS payloads.
“We see drone and cargo could be one of the first use cases that come into play because of the ability to certify and to comply with regulations and to maintain safety at first,” Surace said.
Once Honeywell’s DAA technology is proven and launched effectively for multiple drone use cases at varying sizes, the company will employ its go-to strategy of retooling successful legacy Honeywell innovations for new applications. By design, DAA will set the stage for bringing scaled collision avoidance to larger aircraft usage and to air travel that carries more risk, like manned piloted vehicles and those carrying passengers. The larger goal of fully redesigning the traditional commercial cockpit and setting an early standard for air taxi piloting with SVO is completely dependent on DAA; that larger glide path to autonomous UAM operations is shaping all of Surace and Baker’s work.
Once DAA is air taxi-ready, the radar’s complete set of features will be put to best use. The capacity to support ‘off the beaten path’ flights, emergency landings and other contingency management is useful for small drone deliveries but becomes a heightened safety priority when human lives are involved. For example, Honeywell’s DAA will ideally make sure pilots can pick the right patch of land for touchdown, even in tricky situations.
“Our radar has a capability to not only do air to air, but air to ground…it’ll always be applicable on landing and takeoff. So it has the capability of doing ground mapping so that we can look at the ground and map ground features for landing,” Surace said.
Finally, the goal for DAA is to have a solution that is drone agnostic. Production of DAA payloads for all-custom interfaces would be a massive delay on time-to-market and a strain on Honeywell’s production supply chain. It would also make for inconsistent performance and difficulties in standardizing the cooperation data necessary to run a network of UAS’. Getting that down to a common foundation benefits everyone, especially Honeywell. That’s why Surace and Baker have been working on developing standard set-up configurations, developing an agnostic factory setting for OEMs to easily adjust for their drones’ specific interfaces, and working directly with the OEMs to forward-fit their drones for DAA functionality.
“The radar requires quite a bit of information from the drone for own-ship position. So it requires body motions and accelerations, and we’re going to standardize that so someone could provide that from the drone. If we get that data from the drone, then it’s really just plugging the radar in, and power and those parameters, and you’re off and running,” Surace said.
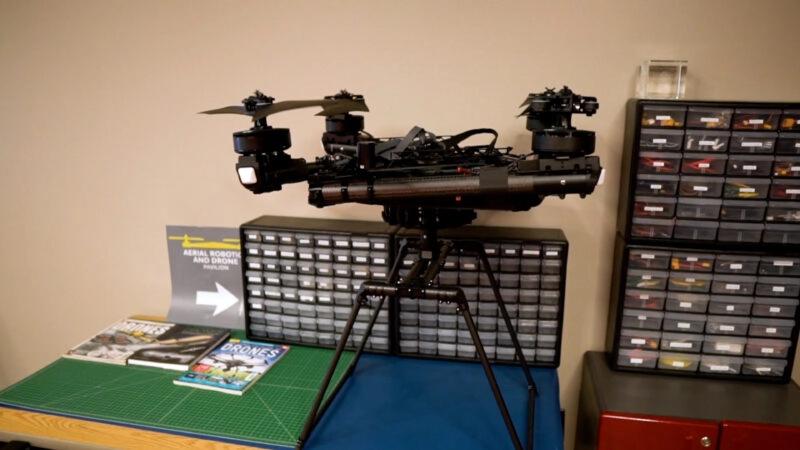
Since the path to full-scale use of DAA is still a long one, Surace, Baker and the Honeywell UAM team have a number of desired features and pressing industry trends shaping their continued DAA research. Here are a few of the stand-outs from our Phoenix visit:
- Testing Against More Obstacles: “We’d like to expand the envelope. We’d like to put multiple drones, multiple intruders against it from different targets, different angles of the targets,” Surace said.
- Preparing DAA for a Wider Geographic Scope: “We didn’t have a lot of geographic area to fly in, we only had a few kilometers that we had to fly in. We had to shrink the whole dynamics of when it had to happen over what period…. And now when we go for our certification effort, we’ll expand that out to meet the requirements of the certification, but it’s dynamic enough to be able to do that,” Surace said.
- New BVLOS Rules: “The rule-making committee has come up with some very good suggestions on how to accelerate that along and how to lower the entry to BVLOS, which I think is good. I think opening markets is a good thing. Our radar will still have applicability in a number of different scenarios,” Surace said.
- Designing a Lighter DAA Payload: “We’re always looking to reduce weight…but not the capability. So the radar that you saw in there is multiboard capability. We’re going to be shrinking that down to just a few boards…. We’re looking to make it smaller, compact. We’re not going to change the face because we want the power aperture. We want the size so that we can detect the targets, but we can take weight out of the heat sink. We can make it smaller. And we also feel that we’ll get better performance because we’ll have more efficiency on transmit and receipt. So we’ll get better range performance. We’re working that every day,” Surace said.
Fly-By-Wire System and Other Under-the-Hood Technologies
What Is It?
SVO and DAA were the stars of the show at Honeywell’s UAM lab reveal, considering their visuals and aesthetic intrigue were captivating all on their own. Of course, their use cases and imagined functionality are the real innovative force that Honeywell is hanging its hat on. But both SVO and DAA would be incomplete without the brains on-board, the unsung foundation for which autonomous air taxi piloting and collision-aware delivery drones are built off of. To manage the growing numbers of electronic processes in UAM platforms from various sensors, meters and pilot inputs, Honeywell developed a first-of-its-kind compact fly-by-wire system.
“Over time, we’ve moved to these fly-by-wire systems, and they call it that because now there is no mechanical linkage. It’s all electrical signal, right? So, when you move this, you’re not physically shortening a cable that’s moving an actuator. You’re just sending electrical signal and that signal moves an actuator,” Fowlkes said.
Fly-by-wire isn’t anything new; the first versions of a digital computer as an aircraft’s main guidance system began their research in the early 1970s. What is new, though, is bringing the functionality of fly-by-wire down to a smaller size without sacrificing any of the capabilities. In fact, preparing fly-by-wire for UAM vehicles is demanding an expansion of features, even with a smaller form factor.
“We’ve taken that exact same capability to the exact same design level assurance, and we put it in a box that’s this size,” Monta said.
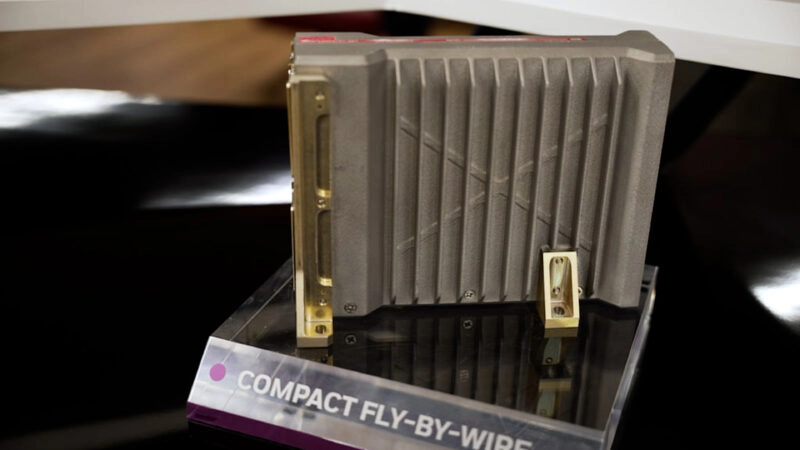
The intended purpose of this compact fly-by-wire system is as simple in vision as SVO and DAA, and just as complex in execution. Since UAS’ operating at scale will have to respond to a number of ground-level and airborne obstacles and will have to do so with reduced or nonexistent pilot inputs, they’ll need an onboard digital computer to make informed and safe maneuvers while performing lockstep processing of coupled flight controls.
“It’s very hard to make one individual adjustment while you’re flying an aircraft on a more traditional system. When you look at what you’ve got by fly-by-wire…you’re actually able to make one independent change at a time without having to do all the other changes,” Fowlkes said.
“It actually looks at all the control laws and then it ensures that the vehicle is doing what you’re intending it to, whether it’s following the flight plan or it’s following your directions,” Shah said.
While most commercial airliners nowadays rock a fly-by-wire system with several layers of redundancy and mechanical backups in case of electrical failure, such a solution is yet to be standardized for the UAM market. Honeywell sees this on-board intelligence as the enabler for realizing its other more visible evolutions to the industry.
Another highlight from the Honeywell UAM lab was its compact SATCOM hardware. Pulling from its experienced pedigree of solutions, its SATCOM device solution was reworked for UAS use cases, and similar to fly-by-wire’s development, Honeywell’s UAS SATCOM research focused on simplifying the mounting, reducing the weight, and developing new use cases for the hardware. Since much of Honeywell’s UAM research is initially focused on deployment for drones, the SATCOM solution was designed to elevate drones into a cooperative communications network and support their most common use cases, like surveying, mapping and first response.
“If you’re out there and you’re saying, ‘Hey, look, I’ve taken video of something or I’ve got some of this other data and I want to share it,’ typically you don’t have any type of internet connection. You don’t have any way to send that data. This small SATCOM system allows you to do that,” Fowlkes said.
Why Research It?
The value of fly-by-wire systems has been validated for decades (even if the industry can sometimes see them as a more expensive option compared to hydraulic or cable systems). Honeywell knows this well, considering it has had a functional fly-by-wire system for commercial airliners for years now. The reason Honeywell invested in developing a new hardware system for the UAM market specifically was two-fold: meeting customers’ CSWaP needs, and fully realizing its commitment to an integrated ecosystem of solutions.
CSWaP needs, which stands for “cost, size, weight, and power,” are a primary motivator for Honeywell; if the company can introduce an on-board computer that is not only scalable for every OEM and its unique flight control laws but is also smaller and doesn’t weigh down the already weight-sensitive aircrafts, then it will have planted another dominant flag in the avionics space. Less weight, and less manual functions between actuators and control inputs, would also keep both operational and maintenance costs low.
“When you look at something like [compact fly-by-wire], it requires less power to run, it’s literally a tenth of the size of a standard fly-by-wire box. And then the cost, and things that go with that, and you get a lot of those efficiencies…. I think it’s a great example of taking something that exists, and that people are familiar with and then putting it down into this size and envelope space that I’d say is appropriate for the UAS space,” Fowlkes said.
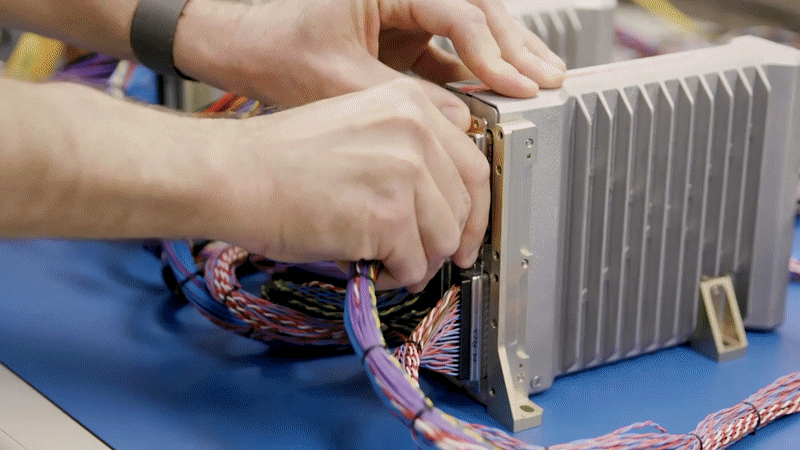
With drone OEMs already working to improve limited flight times and maximize time in the air, Honeywell sees a lighter fly-by-wire system as one of the possible solutions. It would create fuel savings, but on top of that, an emphasis on efficient computing makes for less power draining during complex processing, helping keep drones in the air for as long as possible while performing mission critical functions.
Perhaps more existentially, Honeywell is putting its full faith behind its compact fly-by-wire system because, well, it needs to. Without a UAM-tailored fly-by-wire system, Honeywell won’t be able to launch DAA for more intensive UAS operations, and in turn won’t be able to fully realize SVO. If anything, it makes the fly-by-wire system the most important component in the ecosystem of Honeywell’s UAM research. And as almost every interviewee told us in Phoenix, Honeywell’s true strength as a company shines when its various solutions speak to each other and work together.
“Between the detection and avoid, and the fly-by-wire system, and then the actuators, we’ve got an entire system that says, ‘I see something, I need to get out of the way, I’m going to send a signal to move and then I will actually move the actuators and do it all together,'” Fowlkes said.
How Will It Impact UAM?
What specific functions will Honeywell’s compact fly-by-wire system be most used for? For detect and avoid functions, the on-board computer will be the central hub for interpreting and applying radar data.
“It will take our algorithms, recognize what’s there, decide that it needs to get out of the way, and then it actually will send signal to our fly-by-wire system, which will then move the actuators and actually move the entire aircraft,” Fowlkes said.
For Simplified Vehicle Operation, a compact fly-by-wire system will be essential for all of its core functionality. One of the most important uses will be keeping UAM vehicles within pre-determined safety envelopes, which is not only useful for making sure fully autonomous drones remain stable during flight, but also for adventurous pilots wanting to take their air taxi for a Blue Angels-style spin.
“You’ve got the controllers and you might want to do a barrel roll, cause it feels fun. But the fly-by-wire system recognizes that’s not safe for you or the aircraft and will actually make sure that it keeps you within that safety envelope,” Fowlkes said.
Honeywell already has interest in its fly-by-wire system from the UAM industry, and has even secured partnerships with leading OEMs like Lilium and Pipistrel, both of which are inching closer to successfully bringing an eVTOL to market.
Many of the long-term impacts of a UAM-specific fly-by-wire system are represented by the solutions it’ll support: DAA and SVO. But to reiterate, here’s why Honeywell is placing its faith in a compact fly-by-wire system, and where it sees it playing the most important roles in supporting UAM’s future growth:
- Supporting New Pilots During a Pilot Shortage: “It’s a much more intuitive system. Again, you can sit there for five or 10 minutes, and after a couple of minutes of playing with it, at least be familiar overall with the objectives and a lot of the data that traditionally you needed to know because you were managing it all, you don’t need anymore, because now you’ve got these fly-by-wire systems and some of this integrated system that’s doing a lot of that work for you. So that makes it a lot easier…. Does it encourage more pilots to become pilots? Once they do become pilots, are they trained and up to speed a lot faster,” Fowlkes said.
- Decoupling Flight Controls for Ease of Use: “So if you’re going to roll the aircraft or go up or down, what’s happening to the speed, right? Because those are all coupled, all of the axes are coupled within the vehicle, if you change your altitude it’s going to affect your speed, right? And so, you need to now make sure that you don’t slow down because that’s going to stall the aircraft. So you need to kinda manage all these different axes. In a UAM with a Honeywell fly-by-wire system, all of these things are decoupled. So, if you want to change the speed, you go ahead and change the speed. It’s not going to affect anything else. If you’re going to roll and turn, it’s going to affect only that and the vehicle is going to manage and control everything else, it will make sure that the vehicle never gets into any kind of unsafe condition. So the training required to manage all of that goes down,” Shah said.
How Will Honeywell Stand Out in a Crowded Field?
With its OEM partnerships, successful test flights, and prototype interfaces, Honeywell is well on its way toward finalizing and launching its suite of UAM solutions. The full impact of this research won’t just be felt by Honeywell in terms of new partnerships and sales, nor even just by the UAM market. What Honeywell helps to shape with its avionics solutions will have ripple effects felt all the way down to local urban economies.
COVID’s acceleration of suburban growth is creating a workplace conundrum: If more people are moving outside of city centers, how will this impact commutes and inner-city commerce? Public transit across the US between suburbs and cities is inconsistent at best, if not too spread out and underfunded to be a useful commuting option. Finding new ways to simplify and expand commuting options, and in turn stimulate metropolitan economies by keeping employees working in the city, would have numerous positive consequences.
“If we could take congestion off the roads, if we could move people and enable maybe a greater sprawl so that people could have homes close to the urban activity but not as close as we typically needed to be in order to benefit from either being able to commute in or take public transportation, suddenly you’ve created some economic value,” Newman said. “People could get to work and get home, air taxis, drone taxis, it could open doors. And of course, at the higher end of the market, it’s an economy in itself that, for business travel, private travel, to be able to get people around.”
Honeywell is ahead of the avionics pack in terms of bringing viable avionics at the size and scale needed for the UAM market. That doesn’t mean they’ve outrun them, though. The avionics market is a crowded one, and everyone has their eye on the untapped potential of UAM. The usual aerospace and defense giants Boeing and Northrup Grumman are looking to capture their slice of market share, investing in a “singular, go-to-market” air taxi vehicle and developing their own suite of avionics solutions, respectively.
Even smaller players are hoping to compete with the big dogs and put pressure on companies like Honeywell, including UAM-focused avionics developers like uAvionix and TE Connectivity.
What are some of the ways Honeywell is strategizing to stand out, strategically bring its solutions to market, and maintain its leadership status in UAM avionics?
Quality Production
- “We’ll go through our normal manufacturing readiness review and technology readiness review, and they go through various stages all the way up to production. And then we’ll bring people in from our chief engineers, our center of excellence engineers, our certification engineers,” Surace said.
Quality Relationships
- “We talk to the FAA all the time, they’ve been working with us in a very hand-in-hand process, we understand what they need, they understand how we do things. We don’t just show up at the end and say, here, certify this. We show up as, here’s the end of what we’ve been talking about for a long time, and here’s how it’s safe and this is how it’s built to be reliable and have a high integrity to it,” Surace said.
Agnostic Technology
- “We’re putting together a standard data sheet for the radar…. You open up a box and, ‘okay, here’s the data sheet, and this is how I run it, this is what I need for my vehicle.’ You can have a set of software you can load on your PC, plug in the radar, set the radar up outside of factory settings if you want to, and then it’s really vehicle agnostic after that,” Surace said.
How Can Honeywell Strategically Bring These Solutions to Market?
In speaking with Newman and trading analysis, we brainstormed several of the “stories” that Honeywell could center in its UAM campaigns as it markets its solutions and sells the vision of SVO, DAA, and the entire avionics suite to OEMs and regulators. Here are the ones that stood out the most and that align most immediately with Honeywell’s work:
The ‘Consumer Relatability’ Narrative
- “I also like the fact that they’re looking at taking the equipment and the modernized avionics and making it match more closely to the experience that we’re used to on our iPad, on our PC, on our mobile device and understand that’s how our rising generation understands technology…. I think as sentiment improves, I think as people feel that the newest technologies match the technologies they’re comfortable with, adoption will grow, safety will grow, and by the way, policy regulators can understand it. And I think market relatability matters for Honeywell because I think that’s part of how they get that credit for the contributions they make in the background to the growing aerospace industry,” Newman said.
The ‘Changing Workplace’ Narrative
- “You hear a lot of political ambitions to get jobs into the heartland, get jobs into the rural areas or smaller urban centers. Well, how do you do that? How do you get people to and from…? Everybody might want to migrate and live in those places, but they might want to work in those places if it was accessible. So, it’d be like a massive reverse commute,” Newman said.
The ‘Alternative to Autonomous Vehicles’ Narrative
- “On roads you have, first of all, more congestion…everybody’s on the ground except for birds. And so you’ve got people, you’ve got cyclists, you got pedestrians, you’ve got buildings, you’ve got trees, you’ve got all kinds of lakes and obstructions. In the air, there’s typically less…you can have more I would say airplanes, helicopters, drones flying because of the three dimensions, because you can have different altitudes. So that creates an opportunity to have some reduced complexity,” Newman said.
The ‘UAM as Public Transit’ Narrative
- “It’s really about democracy. At the high end, this will take off. There are people that have the resources and the means, and time is the most valuable asset they have, and they’re happy to spend whatever. But the vast majority of people are stuck in those cabs between JFK and New York City, because you can’t afford to take a $1000 or $10,000 or whatever it costs to get at your own chopper or your own service…. If it could be done at scale and it costs maybe what [an Uber Black] car would cost, suddenly you’ve opened up the market to a whole new segment, you’ve created economic value and you’ve given time back,” Newman said
While Honeywell has a lot to feed its optimism for winning the UAM avionics race, there are plenty of challenges still, both for the company specifically and for UAM at large, that could get in the way:
Market Competition
- “In the middle mile space, I think we’ll see a lot of competitors. There’s a lot of companies that are able to make drones, a lot of the technologies, a lot simpler. And then because you’re just having packages, a lot of the normal regulations would be a little bit simpler. So I think this is an area that we’ll probably see a lot of startups in,” Fowlkes said.
Federal Policy
- “A lot of the technology for autonomous driving is much like what you’re hearing for autonomous travel or urban air mobility, it comes down to the policy. It comes down to the connectivity that these devices all have. Are they able to talk to one another? Are they able to talk to government and local municipalities? Are they able to connect to the cloud and offload data for important management for machine learning to improve and continue to evolve these technologies?… I think companies like Honeywell are going to have to be in the lead of communicating to lawmakers to help them understand that their profile is safe, that the technology is good and that it can scale,” Newman said.
State and Local Subsidies
- “We’re going to need subsidy. We spend taxpayer dollars to build roads and to build infrastructure. This is an infrastructure in itself. And so, if policy makers could understand that economic benefit, not just like I said, life quality, but the true opportunity to employ more people, to bring more jobs, more experiences people in and out of the city and in and out of urban to suburban, to rural, and make greater connections, that’s going to spur economic activity and that economic activity has value. But it’s going to need subsidy,” Newman said.
Achieving True Democratization of UAM
- “I think [UAM public transit] could be a destination, but the path to get there is going to be substantial. This is not going to be something that’s going to be an everyday part of our lives anytime soon. It’s going to be accessible, like I said, to a small component of the population,” Newman said.
While the UAM market’s timeline for mass adoption is yet to be defined, Honeywell will continue full steam ahead with its research into UAM avionics. The company has plans to bring Arizona officials and regulators by the facility to further cement how Honeywell’s solutions can benefit the local economy’s UAM investments. Until OEMs and service providers perfect the air taxi, Honeywell will maintain focus on drone and middle-mile cargo avionics to prove its technologies’ capabilities. As Newman put it, Honeywell will keep telling its technology story behind the scenes; and will keep playing an essential role in the larger societal story of urban air mobility.
Reporting and analysis by Daniel Litwin. Written editing assistance by Gabrielle Bar. Video edit by Hayley Knight. Title card illustration by Garrett Golightly. Additional video footage provided by Honeywell Aerospace.